Biodiesel-Petrodiesel Blends Physicochemical Characterization and Economic Assessment of Designing a Plant in Iran
Omid Koohshekan 1, Alireza Pardakhti 1, Mohammad Ali Zahed 2, Abozar Salehi 1, Zahra Soltanian Zadeh 3*, Amin Mojiri 4
1 School of Environment, College of Engineering, University of Tehran, Tehran, Iran.
2 Faculty of Biological Sciences, Kharazmi University, Tehran, Iran.
3 Environmental Science & Technology Research center, Department of Environmental Health Engineering, School of Health, Shahid Sadoughi University of Medical Science, Yazd, Iran.
4 Department of Civil and Environmental Engineering, Hiroshima University, Japan.
A R T I C L E I N F O |
|
ABSTRACT |
ORIGINAL ARTICLE |
|
Introduction: By substituting conventional fossil fuels, biofuel can emerge as a potential sustainable energy source with favorable environmental outcomes. Biodiesel, in particular, is increasingly attracting attention due to its high potential to increase the consumption of biofuel and contributing to sustainable development. Experimental studies have revealed that biodiesel can play a considerable role of biodiesel in improving petroleum-based characteristics.
Materials and Methods: Physicochemical properties of pure biodiesel produced through esterification and transesterification, petroleum diesel, and biodiesel-diesel blends were experimentally measured. Ninety percent of the filtered and dried waste cooking oil (WCO) was converted to biodiesel, and it was shown that cetane index, flash point, and fire point increased by applying B10 (10% biodiesel + 90% petrodiesel) instead of petrodiesel.
Results: B10 exhibited an adequate depression in pour point and cloud point by 6°C and 3°C at low temperature, respectively. Also, in this study, an economical study and a sensitivity analysis of a biodiesel production plant from WCO with a capacity of 90 tons per day was carried out, using COMFAR III software. The highest proportion of operating cost belonged to WCO (75%) followed by methanol (10%) and machinery, service, and maintenance expense (5%).
Conclusion: Biodiesel showed a positive influence on petrodiesel characteristics, in which the desired green fuel contributed to save the environment. Eventually, economic analysis provides the possibility of running a plant in Iran as a sustainable solution to energy issues. |
Article History:
Received: 19 October 2022
Accepted: 21 February 2023
|
|
*Corresponding Author:
Zahra Soltanian Zadeh
Email:
z.soltanian@ssu.ac.ir
Tel:
+98 2122432040 |
|
Keywords:
Environmental Impact,
Biofuel,
Sustainable Development,
Physicochemical Properties,
Economic Analysis. |
Citation: Koohshekan O, Pardakhti A, Zahed MA, et al. Biodiesel-Petrodiesel Blends Physicochemical Characterization and Economic Assessment of Designing a Plant in Iran. J Environ Health Sustain Dev. 2023; 8(1): 1897-914.
Introduction
Humans have been dealing with environmental pollution as a major problem in the 21st century1, 2. One of the greatest challenges that scientists have faced globally is a gradual increase in conventional fossil-fuel-related pollution and cost, which can be solved by using renewable energy resources 3, 4. Various renewable energy sources such as solar energy, wind, biofuels (biodiesel, bioethanol), and waste heat have been developed to efficiently harvest energy 5-7. Fossil fuel pollution brings about many detrimental effects on human health, such as exhaust emissions containing particle matters (PM), nitrogen oxides (NOx), carbon monoxide (CO) and unburned hydrocarbons (HC), which can cause lung cancer, lung oedema, fatal effects on fetuses, and morbidity promotion 8-10.
Biodiesel production from waste cooking oil (WCO) is an effective strategy for decreasing the cost of raw material, as well as solving the waste oil disposal problem 11-14. It is noticed that low price and availability of waste oil make it more preferable than vegetable oil, either edible or non-edible. High viscosity of the waste oil is the main deterrent to using it directly in combustion systems. Three different methods of thermal cracking, pyrolysis, and trans-esterification have been suggested to reduce viscosity 15, 16. Low cost and high conversion efficiency have made trans-esterification more desirable for practical purposes 17.
Several advantages of biodiesel over fossil fuel such as biodegradability, non-toxicity, greenhouse gasses reduction, similarity to petroleum-based diesel structure, and the ability to mix with petrodiesel at different portions are principal reasons for its rising consumption. Moreover, lack of sulfur and aromatics, and less pollution due to the existence of oxygen in its chemical structure turns it into an environmentally friendly fuel 18, 19.
Biodiesel contains mono-alkyl ester of a long- chain saturated and unsaturated fatty acids, and its composition consists of 75% C, 13% H, and 12% O by weight, in which the presence of oxygen influences the performance of engine 20-22. The fewer C-H bonds as a consequence of high concentration of oxygen leads to lower CO and HC emissions. Besides, burning smoothly and high evaporation rate can be counted as the advantages of using biodiesel 23, 24. Cloud point and pour point can be considered significant advantages of biodiesel, which improve the cold-flow properties of the fuel25. Therefore, biodiesel has a good potential to use in the transportation sector as an alternative fuel and also in power plants26.
Recently, biodiesel is drawing the attention of south-east Asian countries. In this area, B5 biodiesel blend taken from palm oil is used for transportation as well as power generation and in the industrial sectors. Malaysia is a country that has reached high levels in biodiesel production by using jatropha and palm oil, and is currently attempting to formulate a richer blend ratio 27.
Currently, studies are focused on cheaper feedstock for biodiesel production, such as WCO, waste animal fat, and sewage sludge. Capodaglio and Callegari concluded that waste sewage sludge can be a suitable raw material for biodiesel production, which has a much lower cost by using pyrolysis28. Moecke et al. evaluated economic, environmental and social aspects of biodiesel, reporting that the produced biodiesel can be used as fuel in the artisanal fishing boats. Trans-esterification process was applied for biodiesel production from WCO in a batch reactor
with a capacity of 200 (Lday ) 29. In addition, based on life cycle assessment (LCA) studies, socioeconomic advantages and environmental effects of biodiesel were analyzed using a pilot plant for required processes in order to produce biodiesel from WCO gathered in Brazil30. However, comparing laboratory and large-scale data, LCA studies have provided good information on the cultivation and harvesting of algae. Results have demonstrated favorable environmental outcomes regarding particulate matter, global warming, and total NOx and SOx emissions 31.
In Iran, replacing conventional fuel with renewable energy from biomass sources such as citrus waste products gives a higher benefit and has a great potential for biodiesel production, bioethanol, and biogas 32, 33. It should also be noted that biodiesel production has been studied technically and economically by authors in Iran, who considered waste oil to be an affordable resource 34-37.
Biofuel has great potential in Iran, since about 7% of the territory is covered with forests, which can produce valuable resources such as lipids. Algae, fish oil, as well as plant oil sources such as jatropha, castor plant, and palm. These are suitable sources for biodiesel production, especially WCO, of which 0.3 million tons is produced annually. Therefore, this appealing setting provides strong evidence that it is quite enough to forecast blending ratios up to B10 by 2026 38.
China, USA, India, and Russia are the leading CO2 producers in the world39. Iran emitted 3.6 tons CO2 per capita in 1990, which reached 5.3 tons in 2000. This amount of pollution rate has grown in recent years to reach 7.56 tons per capita in 201540.
The objective of this study is to evaluate the specification of WCO methyl ester (biodiesel, B100) and conventional petrodiesel fuel (B0) as well as biodiesel blends. WCO as a low-cost raw material was used experimentally to produce biodiesel. Moreover, B10 in Iran, as an alternative to petrodiesel, is anticipated to be highly promoted by 2035. Due to its enormous potential to expand the consumption of biofuel and contribute to sustainable development, biodiesel is gaining more and more attention. Moreover, a factory with a capacity of 90 tons per day was examined
economically.
Materials and Methods
Methodology
WCO was obtained from several local restaurants and then mixed in order to make feedstock for biodiesel production process. Figure 1 shows the biodiesel production apparatus for both esterification and trans-esterification, which consists of 6 items. The pilot of desired reaction process was equipped with a reflux condenser, 500 ml three-necked flask, heater stirrer, magnetic stirrer, water bath, and a thermometer. The reagents applied in the experiment conditions of biodiesel production are presented in Table 1. The yield of fatty acid methyl ester (FAME) was calculated by equation (1), which is mentioned below 41:
yield %=[weight of biodiesel g/weight of lipid g] ×100 (1)
Biodiesel production
Biodiesel production process is performed in four steps:
1. Waste oil filtering and preparation
Gathered waste oil needs an impurity separation process. To this end, as shown in Figure 2 (a), suspended food particles should be separated by filtering through filter paper. Absence of water results in the prevention of soap production, which is undesirable for biodiesel production. The reaction of water and alcohol reduces process yield and makes the final separation difficult. Hence, it was placed on a hot plate at a temperature above 100 °C stirring for an hour to eliminate water content in the waste oil.
2. Esterification and transesterification reactions
Heating oil decomposes the long carbon chain to create free fatty acids 42. The reaction of free fatty acids with alkali catalyst produces soap, and water which decreases the outcome of reaction and forms the emulation 43, 44. An acid-catalyzed technique was used in biodiesel production to decrease the content of free fatty acid (FFA) to less than 1% in order to convert FFA into methyl ester until WCO was prepared for the trans-esterification process by base-catalyst 45-47. A titrimetric method was applied to determine the FFA content representing an amount of 5.37 wt. %. In the acid-catalyzed process, 100 ml filtered oil with 8:1 molar ratio of methanol (purity 98%) to oil and 1% (v/v) of H2SO4 (98%) were applied to the crude oil. As shown in Figure 2 (b), the reaction was carried out at 75 °C and 800 rpm. After 2 hours, a separating funnel was used to separate the acid, impurity, and methanol. After 10 hours, the lower layer (esterified oil) was separated and entered into a rotary evaporator. It can eliminate almost all water and alcohol excess after 1 hour. Then, to perform transesterification reaction, processed waste oil (at 50 °C) again was poured into three neck-round flasks equipped with a reflux condenser and a thermometer (Digital thermometer (KT-300) 240x30x30 mm, accuracy -50 to 300 Celsius) to avoid alcohol vaporization, then a combination of 25 ml of methanol and 0.5% w/w (of oil) sodium hydroxide (99%) was added to the flask. The reaction was allowed to proceed at 70 °C (± 2) with continuous stirring at 600 rpm for 1.5 hours and refluxing by a water-cooled condenser. According to the color change and return of alcohol from the condenser in the first 45 minutes, it seems that most of the conversions took place in this period.
3. Separation of biodiesel and glycerol:
When the reaction was complete, the mixture was passed through to the separating funnel for a day to separate the rich phase of glycerol from biodiesel. There might be some excess impurities in the lower layer which has to be removed. It can be seen in Figure 2 (c).
4. Post-treatment process
It was probable that the biodiesel still contains glycerol, alcohol, and impurities. Therefore, as shown in Figure 2 (d), the sample was heated up to 75 °C with continuous stirring for half an hour to vaporize alcohol, and then it was washed with warm distilled water at least three times until the outlet water became slightly clear. In the next stage, excess water and methanol were eliminated by a rotary evaporator. Finally, the remaining water was taken from biodiesel by heating and using granular Na2So4 . Eventually, a filter paper (150 mm diameter, no.1) was employed to filter the final product which was prepared for blending with ordinary diesel.
.PNG)
Figure 1: Schematic diagram of biodiesel production setup
Table 1: Summary of processes of biodiesel production from WCO
|
Parameter |
Specification |
Esterification |
Transesterification |
Source |
WCO |
|
Alcohol used |
Methanol |
98 % purification Merck |
Catalyst used |
H2SO4 |
NaOH |
Acidic catalyst: 98%
Alkali catalyst: 99% |
Reaction temperature |
75 °C |
70 °C |
- |
Reaction time |
2 h |
1.5 h |
- |
Stirring speed |
800 rpm |
600 rpm |
- |
.PNG)
Figure 2: (a) Waste oil filtering, (b) Reaction system, (c) Separating funnel, and (d) Purification
Blending of biodiesel
It is not common to use neat biodiesel because of economic disadvantages, incompatibility with engines, and physicochemical issues, such as low energy content, oxidation stability, higher kinematic viscosity, and density. Petro-diesel can be completely miscible to biodiesel at different portions 48, 49. Biodiesel blend at different ratios is a suitable choice to improve the quality of conventional petrodiesel. Therefore, these blends were supplied to verify the effect of blending on petrodiesel based on ASTM D6751 standard procedure.
Petro-diesel was prepared from Tehran refinery based on Euro 5 standard. In order to make blends at three different ratios including B5, B10, and B20 by volume fraction, they were mixed under following appropriate conditions and are shown in Figure 3. To make these blends, a 500 ml neck-round flask was used and biodiesel was added to petroleum-based diesel at 45 °C. The flask was fixed with a clamp on a vertical stand with continuous stirring at a speed of 700 rpm for 1 hour.
.PNG)
Figure 3: Biodiesel Blends: B0, B5, B10, B20, and B100
Physicochemical analysis
Physical and chemical characteristics of biodiesel and biodiesel/petro-diesel blends were analyzed using ASTM D6751 method.
Economic analysis
The production steps of biodiesel on a laboratory scale and chemical parameters in its characteristics are described in the previous section. Then, a WCO biodiesel plant was evaluated economically with a capacity of 90 tons per day. Economic estimates of factory construction and internal rate of return (IRR) sensitivity analysis were performed by COMFAR III software on a variety of parameters.
COMFAR software has been designed by
the United Nations Industrial Development Organization (UNIDO) to evaluate economic projects. The software makes it easy to organize and calculate financial reports. The advantages of COMFAR software include high flexibility, user-friendliness, low error, and high level of sensitivity.
Results
Characterization of fuel properties
The percentage of biodiesel yield (lipid conversion efficiency) obtained from optimum reactions was 90% after eliminating glycerol from separating funnel. Table 2(a), (b) shows the properties of produced biodiesel (B100) in comparison to other studies and demonstrates the chemical and physical properties of the blends such as kinematic viscosity at 40 °C, density, pour point, cloud point, flash point, fire point sulfur content, cetan index, and calorific value. These results are in accordance to the standard test method ASTM D6751, and the data depicted in Table 2 are expressed as an average of three values in each test.
Table 2(a): Biodiesel obtained from WCO characterization
Properties |
Unit |
Test method |
ASTM-BD D6751 |
N. Yilmaz et al. 50 |
Z. Al-Hamamre, A. Al-Salaymeh 51 |
A.N. Phan, T.M. Phan 52 |
Sadaf et al. 53 |
Produced Biodiesel
(this study) |
Kinematic viscosity at 40 °C |
mm2/s |
D445 |
1.9 - 6.0 |
4.57 |
5.86 |
4.89 |
5.83 |
5.8 |
Density at 15 °C |
kg/m3 |
D4052 |
860 to 900 |
855 |
877 |
880 |
874 |
870 |
Pour point |
°C |
D97 |
-15 to 10 |
|
|
0 |
1 |
9 |
Cloud point |
°C |
D2500 |
|
|
|
3 |
10.5 |
21 |
Flash point |
°C |
D93 |
130 min |
126 |
150 |
120 |
|
144 |
Fire point |
°C |
D92 |
|
|
|
|
|
198 |
Cetan index |
|
D976 |
|
|
|
|
|
59.7 |
Sulfur content |
ppm |
D4294 |
15 ppm |
|
|
|
|
12 |
Calorific value (HHV) |
MJkg |
D240 |
> 35 |
40.5 |
35.66 |
41.84 |
37.2 |
45.11 |
Table 2(b): Physicochemical fuel properties of biodiesel in comparison to petrodiesel and its blends
Properties |
Unit |
Test method |
B0
(Petrodiesel) |
B5
(5 % v/v) |
B10
(10 % v/v) |
B20
(20 % v/v) |
B100
(Biodiesel) |
Kinematic viscosity at 40 °C |
mm2/s |
D445 |
2.75 |
2.83 |
3.04 |
3.1 |
5.8 |
Density at 15 °C |
kg/m3 |
D4052 |
821 |
823 |
827 |
834 |
870 |
Pour point |
°C |
D97 |
-6 |
-8 |
-12 |
-12 |
9 |
Cloud point |
°C |
D2500 |
2 |
0 |
-1 |
-2 |
21 |
Flash point |
°C |
D93 |
63 |
63.5 |
64.5 |
66 |
144 |
Fire point |
°C |
D92 |
91 |
92 |
93 |
94.5 |
198 |
Cetan index |
|
D976 |
55.9 |
56.1 |
56.4 |
57.1 |
59.7 |
Sulfur content |
ppm |
D4294 |
56 |
55 |
52 |
48 |
12 |
Calorific value (HHV) |
MJkg |
D240 |
45.98 |
45.91 |
45.89 |
45.79 |
45.11 |
Fuel properties analysis
The following section discusses the properties of blending pure biodiesel with conventional petroleum-based diesel.
Density
Density is an important property of fuel atomization and affects the energy content, air-fuel ratio within the diesel engine and cetan number 54, 55. Figure 4 presents the variation in density with volumetric percentage of biodiesel-petro diesel. The foregoing density for petro-diesel goes up from 821 to 823, 827, and 834 (kgm3) for B0, B5, B10, and B20, respectively. Thus, it can be seen that blend density increased slightly by increasing the biodiesel percentage.
Kinematic viscosity at 40 °C
One of the fuel properties affecting the fuel injection system is kinematic viscosity. Fuel fluidity and atomization are important characteristics of fuels measured by kinematic viscosity 56, 57. Unsuitable fuel injection and pumping can cause incompetency at low temperatures due to higher kinematic viscosity 58. The kinematic viscosity of biodiesel was measured at 5.8 (mm2/s) , and the recommended range of kinematic viscosity is 1.9- 6.0 (mm2/s) according to ASTM test method 57. It was observed experimentally that the kinematic viscosity at 40 °C of petro-diesel increased when the biodiesel portions in petro-diesel rose (Figure 4). The kinematic viscosity changed from 2.75(B0) to 2.83, 3.04, and 3.10 (mm2/s) for B5, B10, and B20, respectively.
.PNG)
Figure 4: Density and kinematic viscosity of blends
Calorific value (MJkg)
The energy content of biodiesel is known as the potential energy contained in a given biodiesel fuel influencing the engine power, which depends on the energy content of the oil as a feedstock 42, 59. In this investigation, the energy content known as higher heating value (HHV) of methyl ester was measured and the results are presented in Table 2. Figure 5 shows blended biodiesel energy is slightly less than petrodiesel. An increase in biodiesel-diesel blend ratios marginally decreased the calorific value of the blends. The calorific value of the biodiesel was measured 45.115 (MJkg) which was 98.11 % of the petro-diesel (B0) and the energy quantity of B5, B10, and B20 were found 0.13%, 0.18%, and 0.4% less than petro-diesel, respectively, as reported in Table 2(b). Therefore, considering the final cost of biodiesel blends, HHV is an important characteristic of a fuel, which indicates the upper limit of the available thermal energy produced by a complete combustion of fuel. It may not be reasonable to mix higher amounts of biodiesel to maintain the adequate expected energy content; therefore, B0 to B10 would be logical options.
.PNG)
Figure 5: Calorific value (HHV) of biodiesel blends
Cetane index
In another experimental investigation, cetane value of fuel was evaluated to measure the ignition quality. The ignition delay time is the period that fuel is injected and began to combust. During this time the fuel evaporates and is dispersed with
the compressed air in the combustion chamber.
If all conditions are available, the fuel will spontaneously begin to combust. The ignition time depends on the composition of the fuel, operational parameter, and engine design. Cetane is the speed of fuel combustion and an indicator of fuel quality. The lower cetane values have a longer ignition delay compared to the higher ones. Cetan index is an essential property since biodiesel affects the petrodiesel cetan index. The recommended cetane index range for biodiesel/petrodiesel blends is at least 40 60. In this study, B0 cetan index was found 55.9 and attained 56.1, 56.4, and 57.1 for B5, B10, and B20, respectively (Table 2 and Figure 6).
Sulfur content
Due to the lower sulfur content in biodiesel compared to petrodiesel, lower amount of SO2 is produced 61. Sulfur content of diesel fuel depends on fuel types and varies from one engine to another. Sulfur is known as an emission causing acid rain, and affects PM emissions to the extent that has convinced the scientists to limit diesel sulfur content more than ever. Sulfur subtraction needs to be taken into account because it can increase ecosystem damage and cause lots of losses in the country. As a result, new technologies of emission control and heavy processing have been performed at Tehran refinery to reduce sulfur content in recent years.
The biodiesel sulfur content was measured 12 ppm, while the proposed value of the sulfur-based fuel on ASTM D6751 standard is reported less than 15 ppm62. The results show that biodiesel as an additive can reduce the sulfur content of petrodiesel from 56 ppm (B0) to 52 ppm (B10). Sulfur content reduction trend is given in Table 2 and it can be seen in Figure 6.
.PNG)
Figure 6: Cetan index and sulfur content of biodiesel blends
Flash point and Fire point (°C)
The flash point shows the minimum temperature at which fuel vaporizes enough to get ignited, and is known as the safety measure of fuels for transportation and storage. The fire point is the lowest temperature at which the vapor of fuel continues to burn for at least 5 seconds after ignition 63, 64. Table 2 demonstrates a slight increase in several percentages of biodiesel in the blends and a drastic two-fold rise in 100% biodiesel compared to ordinary fuel. The flash point and fire point of petrodiesel were measured 63 and 91°C, respectively. Figure 7 demonstrates that the flash point and fire point increase as the blend ratios increase. The flash point of 100% biodiesel complied with ASTM D6751, and it had the highest flash point indicating low volatility of this fuel 65. Mixing biodiesel with petro-diesel can increase the flash point of the blends and is a suitable choice in terms of safety, since higher flash point of biodiesel decreases flammability hazard providing more safety in transferring and shipping. So, increasing the rate of biodiesel positively enhances the safety regulation of introduced fuel.
.PNG)
Figure 7: Flash point and fire point of biodiesel blends
Pour point and cloud point (°C)
Fuel constraints under cold weather are generally determined by factors such as cloud point, pour point, and cold filter plugging point. Cloud point shows the temperature at which the cluster of wax crystal can be seen, and the temperature at which fuel flow reduces due to gel formation during fuel cooling is known as the pour point of fuels 66. The pour point and cloud point of WCO methyl ester were measured at different mixing portions as represented in Figure 8 and Table 2. Biodiesel (B100) had a higher pour point and cloud point in comparison with petrodiesel (B0), 9°C, and 21°C, respectively. It is important to notice that biodiesel can decrease these characteristics by making blends; in other words, both cloud point and pour point of biodiesel blends were lower than conventional petrodiesel. According to Table 2, B10 had lower pour point and cloud point than petro-diesel enabling higher compatibility with vehicles.
.PNG)
Figure 8: Pour point and cloud point of biodiesel blends
Distillation curve (°C)
Fuel tendency to form smoke and soot is evaluated by distillation curve 67. Fuel distillation significantly impacts fuel safety and performance, since volatility has a profound effect on fuel tendency to vaporize, especially initial boiling point (IBP), which influences fuel vapor pressure 68. According to Table 3 and Figure 9, the distillation curve is the temperature change as a function of distillation percentage from IBP to final boiling point (FBP), performed at the atmospheric pressure of fuel.
In this survey, ASTM D86 was used for obtaining experimental distillation, because at different percentages of recovery, biodiesel has the highest distillation temperature. The obtained results showed that the percentage of biodiesel had direct relationship with IBP and FBP. The IBP of biodiesel was measured at 261 °C, while conventional diesel had the lowest value of 175 °C. IBP was measured at 170.5, 171, and 172 °C for B5, B10, and B20, respectively. According to Table 3, boiling point at 10% to 95% recovery of each sample was higher in contrast to petrodiesel (B0). It can be demonstrated that at the IBP and FBP the samples temperatures converge, while they diverge as they reach an equal content of each fuel in blends.
.PNG)
Figure 9: Distillation curve of biodiesel, diesel, and the blends
Table 3: Distillation temperature for biodiesel, petrodiesel, and the blends
Vol. % |
B0 |
B5 |
B10 |
B20 |
B100 |
IBP* |
170 |
170.5 |
171 |
172 |
261 |
10 |
197.4 |
198 |
198.5 |
200.5 |
302 |
20 |
210.5 |
213 |
216 |
221 |
312 |
30 |
226 |
231 |
239 |
246 |
317 |
40 |
244 |
249 |
258 |
266.5 |
322 |
50 |
261 |
268 |
276.5 |
286.5 |
327 |
60 |
280.5 |
287 |
294.5 |
302 |
332 |
70 |
296.5 |
304 |
312 |
319 |
340 |
80 |
317 |
321 |
327 |
332 |
345 |
90 |
339 |
341 |
345 |
347 |
365 |
95 |
356 |
359 |
363 |
364 |
372 |
FBP** |
372 |
366 |
368 |
369 |
379 |
* Initial Boiling Point
** Final Boiling Point
Economic assessment of biodiesel production
From an economic viewpoint, WCO is the best raw material in contrast to the utilization of imported fresh edible oil, when only 10-15% of consumed edible oil in Iran is produced by domestic production and the rest is imported 69. It is not reasonable to neglect this large amount of purchased edible oil. According to results, biodiesel production includes the expenses of raw materials, energy, human labor, services, and maintenance.
Not only would the daily consumption of 80 million liters of petrodiesel in Iran be reduced by 10%, but also it can be replaced by an alternative fuel. Therefore, biodiesel would potentially own an 8 million litter market per day. Regarding the capacity of producing biodiesel from WCO, B10 can be produced in order to be consumed in big cities that are receiving the most exposure to pollution (Tehran, Mashhad, Karaj, Esfahan, Shiraz, etc.). For instance, the amount of WCO in Tehran has come to 60000 kg per day only by the food service industry and food manufacturing. As a result, this amount of waste oil is an indigenous threat to ecosystem of Tehran. Regarding the potential of Tehran as a sources of raw material and operationalization, this city can be a suitable option for launching biofuel production. Therefore, B10 is anticipated to be highly promoted as a substitute for petrodiesel by the year 2035 in Iran.
For the economic evaluation, a discount rate of 18% (tax rate = 9%) was assumed for the survey. According to oil conversion efficiency to biodiesel of 90% and biodiesel density of 870kg/m3 , the annual increase rate of operating costs, the annual increase rate of biodiesel price, and the annual increase rate of glycerol price were considered 17%, 2%, and 17% respectively, as inputs to the COMFAR III software. Operational costs and distribution expenses of biodiesel production from WCO are presented in Table 4 and Figure 10, respectively. According to Table 4, unit cost of biodiesel production in Iran is anticipated to be 0.412$L . Figure 10 indicates that the highest share of expenses belongs to WCO (75%), followed by methanol (10%), machinery, services, and maintenance (5%). Moreover, Table 5 shows the total investment costs, and Table 6 demonstrates the revenues from the sale of biodiesel and glycerol. As shown in Figure 11, the largest share of total investment costs belongs to process equipment (62 %), followed by contingencies fees (15%) and utility (9%), respectively. According to economic calculations performed by COMFAR III software, Net Present Value (NPV) of Total Capital Invested (at 18%) was obtained 11,722,000 $, and the IRR on investment was assessed 20.21 % with a 5-year normal payback. Overall, positive net present value (NPV) ($11,722,000) and IRR indexes of more than 18% (21.20 %) can be found, which indicates that the process would be financially feasible.
Table 4: Operating costs for a 90 t/d WCO-biodiesel plant
Item |
Unit |
Price ($/unit) |
Quantity
|
Total cost ($) |
Direct Costs |
|
WCOa |
Tone |
300b |
33000 |
9900000 |
Methanola |
Tone |
215 |
6005 |
1291075 |
H2SO4a |
Tone |
270 |
341.2 |
92129 |
NaOHa |
Tone |
1370 |
37.95 |
51991 |
H2Oa |
M3 |
0.18 |
39930 |
7187 |
Electricitya |
Kwh |
0.07 |
1724910 |
120744 |
Machinery, service and maintenance (10% of process equipment utility equipment, building and structure) |
676900 |
Royality |
|
425000 |
Laborc |
Person |
9240 |
9 |
83160 |
Depreciation |
|
|
|
486554 |
Total direct costs |
|
13134740 |
Indirect costs |
|
Insurance |
|
88160 |
Marketing (2% of total revenue from biodiesel and crude glycerol sale) |
|
837390 |
Total indirect costs |
|
925550 |
Total operating costs |
|
14060290 |
Unit cost of biodiesel production |
|
0.412$/L |
a All given prices are based on Iran market data (2020 April).
b 25 % of fresh vegetable oil price.
c Including basal labor payment and other expenses based on Iran ministry of labor laws.
Table 5: Total capital cost for a 90 t/d WCO-biodiesel plant
Item |
Cost (Thousand USD) |
Equipment |
|
Process equipmenta |
5198 |
Utility equipment |
806 |
Total equipment cost |
6004 |
Civil and constructiona |
|
Land acquisition |
55 |
Building and structure |
161 |
Total civil cost |
216 |
Installationb |
600 |
Contingencies feec |
1283 |
Pre-production expenditures |
302 |
Total capital cost |
8405 |
a All given prices are based on Iran market data – 2020 April.
b 10% of equipment costs including engineering design cost, construction labor, piping, electrical. and control instruments and their programing and other expenses.
c 18% of total equipment cost and civil and construction cost (expect land expense)
Table 6: Total revenue from crude biodiesel and glycerol sales
Sale($) |
Price ($/ton) |
Quantity ( tone) |
31654260 |
1065/8 |
Biodiesel: 29700 |
1032000 |
240 |
Glycerol: 4300 |
.PNG)
Figure 10: Distribution of expenses in biodiesel production
.PNG)
Figure 11: share of different items in total investment costs
Sensitivity analysis
COMFAR III was used for sensitivity analysis. Results indicated that the increase in the internal rate of return had the greatest effect on sales revenues, so that with an increase of 20% in IRR, sales revenues attained 35.57% (Figure 12). Also, it can be seen that the growth in IRR has resulted in a slight increase in fixed assets and led to an extreme decrease in operating costs.
Scope for further research
Authors have recently focused on modern technologies to reduce energy consumption, increase efficiency, and use environmentally-friendly reagents. Accordingly, the mechanochemical approach would be a promising technique, due to improving the reaction conditions in lower temperatures and consuming less time. Therefore, one of the main goals of sustainable development can be reached through mechanochemical processes in biodiesel production.
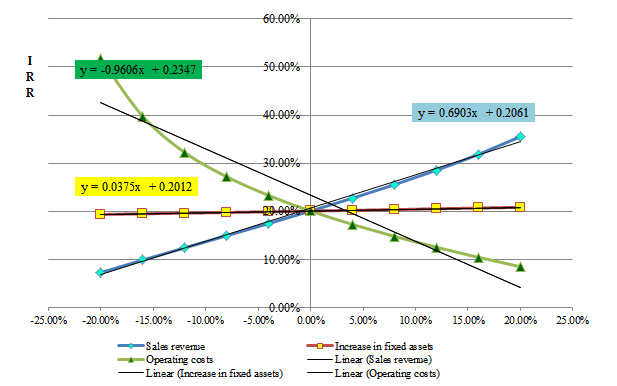
Figure 12: Sensitivity of the IRR on the sales revenue, operating costs and increase in fixed assets
Discussion
In the present study, the production of biodiesel was conducted on laboratory scale, and it was shown that the evaluated properties of the biodiesel conform to the American Society test method standard (ASTM D6751) which is similar to a study conducted by Sadaf, et al. 53. From a technical viewpoint, it is noticed that both the density and viscosity of petrodiesel increase when the blends percentage ratio rises; however, energy content of higher-biodiesel-ratio fuel shows an insignificant decrease which can still provide enough energy in engines. On the other hand, the increased cetane index can play a positive role to enhance the quality of burning, which is achieved by adding more biodiesel in petrodiesel. Higher content of biodiesel in conventional fuel improves the quality by decreasing sulfur content and safety parameters, which are flash point and fire point, making it a favorable fuel in harsh conditions. Furthermore, it was evidenced that the improved pour point and cloud point can work positively in cold conditions to keep the fuel from forming wax crystals as can be seen in Atabani et al. investigation66.
The ever-increasing greenhouse gas (GHG) rate, which is considered a threat to the environment, is an important issue. In the Iranian national document of the knowledge-based development of renewable energy, biodiesel consumption is a part of the renewable energy domain in the 1404 outlook. One of the macro policies of Iran in the exhibition of bioenergy fuels is the consumption of bioethanol and biodiesel in upcoming years. Also, reducing at least 10 million tons of greenhouse gas emissions in comparison with 2015 is expected by increasing the renewable energy share. Therefore, biofuel, as a prerequisite for economic activities, has become one of the most essential elements in global policies in Iran toward sustainable development. Using WCO as raw material for biodiesel production has been considered not only as a progressive step in reducing environmental pollution, but also as a viable measure to improve human safety 25,30.
Conclusion
Due to the growing environmental concerns over the past years, decisions have been made to achieve sustainable development. While developed countries have made considerable progress in controlling environmental pollution, developing countries (e.g. Iran) are still facing different challenges. Waste cooking oil as a cheaper alternative reduces GHG emissions and prevents waste accumulation19. Biodiesel blends are beneficial from an environmental perspective to improve the fuel’s physicochemical properties; hence, biodiesel blends in Iran have advantages including less consumption of conventional fuel, carbon marketing and reducing environmental pollutants. Moreover, it decreases the dependence on imported oil, due to agricultural development, and creates more occupations in the country, leading to new green policies and sustainable development. The ten percent blend of biodiesel with petrodiesel (B10) improves most of the conventional diesel fuel properties, which can be used without any engine modification. Lowering the amount of sulfur can improve environmental health as a result of using biofuels, to meet one of the fundamental objectives of sustainability.
Economic estimation of factory construction and the IRR sensitivity analysis were conducted on a variety of terms. They indicate that the cost of producing biodiesel in Iran reaches 0.412$L . The highest proportion of operating costs respectively belong to WCO (75%) followed by methanol (10%) and machinery, services and maintenance expenses (5%). Moreover, the largest proportion of total investment costs relates to processing equipment (62 %), followed by contingencies fees (15%) and utility (9%).
Sensitivity analysis results show that the increase in the IRR has the greatest effect on sales revenue, while the increasing trend in IRR has resulted in a slight increase in fixed assets, and eventually it leads to an extreme decrease in operating costs. Ultimately, the IRR of more than 18% (21.20 %) and positive NPV indexes ($11,722,000) can be concluded that the project would be economically feasible.
Abbreviations
GHG: Green House Gases
B0: 0% Biodiesel + 100% Petrodiesel
B5: 5% Biodiesel + 95% Petrodiesel
B10: 10% Biodiesel + 90% Petrodiesel
B20: 20% Biodiesel + 80% Petrodiesel
B100: 100% Biodiesel + 0% Petrodiesel
WCO: Waste Cooking Oil
PM: Particle Matters
NOx: Nitrogen Oxides
CO2: Carbon Dioxide
CO: Carbon Monoxide
HC: Hydro Carbons
LCA: Life Cycle Assessment
Sox: Sulfur Oxides
FAME: Fatty Acid Methyl Ester
FFA: Free Fatty Acid
IRR: Internal Rate Of Return
HHV: Higher Heating Value
IBP: Initial Boiling Point
FBP: Final Boiling Point
NPV: Net Present Value
UNIDO: United Nations Industrial Development Organization
Acknowledgment
The authors would like to thank the University of Tehran Science and Technology Park.
Funding
This research did not receive any specific grant from funding agencies in the public, commercial, or not-for-profit sectors.
Conflict of interest
The authors declare there is no conflict of interest.
This is an Open-Access article distributed in accordance with the terms of the Creative Commons Attribution (CC BY 4.0) license, which permits others to distribute, remix, adapt, and build upon this work for commercial use.
References
1. Song Y, Yang T, Li Z, et al. Research on the direct and indirect effects of environmental regulation on environmental pollution: Empirical evidence from 253 prefecture-level cities in China. J Clean Prod. 2020;269:122425.
2. Ahmadi A, Das B, Ehyaei M, et al. Energy, exergy, and techno-economic performance analyses of solar dryers for agro products: A comprehensive review. Solar Energy. 2021;228:349-73.
3. Arshad M, Bano I, Khan N, et al. Electricity generation from biogas of poultry waste: An assessment of potential and feasibility in Pakistan. Renew Sustain Energy Rev. 2018;81:1241-6.
4. Rahimi M, Catalini G, Hariharan S, et al. Carbon dioxide capture using an electrochemically driven proton concentration process. Cell Rep Phys Sci. 2020;1(4):100033.
5. Demirbas A. Biodiesel production from vegetable oils by supercritical methanol. Journal of Scientific & Industrial Research. 2005;64(1):858-65.
6. Chang J, Leung DY, Wu C, et al. A review on the energy production, consumption, and prospect of renewable energy in China. Renew Sustain Energy Rev. 2003;7(5):453-68.
7. Correa SM, Arbilla G. Carbonyl emissions in diesel and biodiesel exhaust. Atmos Environ. 2008;42(4):769-75.
8. Zhang Z, Cheung C, Chan T, et al. Experimental investigation of regulated and unregulated emissions from a diesel engine fueled with Euro V diesel fuel and fumigation methanol. Atmos Environ. 2010;44(8):1054-61.
9. Okona-Mensah K, Battershill J, Boobis A, et al. An approach to investigating the importance of high potency polycyclic aromatic hydrocarbons (PAHs) in the induction of lung cancer by air pollution. Food Chem Toxicol. 2005;43(7):1103-16.
10.Borugadda VB, Paul AK, Chaudhari AJ, et al. Influence of waste cooking oil methyl ester biodiesel blends on the performance and emissions of a diesel engine. Waste Biomass Valorization. 2018;9:283-92.
11.Lin YC, Hsu KH, Chen CB. Experimental investigation of the performance and emissions of a heavy-duty diesel engine fueled with waste cooking oil biodiesel/ultra-low sulfur diesel blends. Energy. 2011;36(1):241-8.
12.Nisar N, Mehmood S, Nisar H, et al. Brassicaceae family oil methyl esters blended with ultra-low sulphur diesel fuel (ULSD): Comparison of fuel properties with fuel standards. Renew Energy. 2018;117:393-403.
13.Dhawane SH, Karmakar B, Ghosh S, et al. Parametric optimisation of biodiesel synthesis from waste cooking oil via Taguchi approach. J Environ Chem Eng. 2018;6(4):3971-80.
14.Cholapandian K, Gurunathan B, Rajendran N. Investigation of CaO nanocatalyst synthesized from Acalypha indica leaves and its application in biodiesel production using waste cooking oil. Fuel. 2022;312:122958.
15.Oh PP, Lau HLN, Chen J, et al. A review on conventional technologies and emerging process intensification (PI) methods for biodiesel production. Renew Sustain Energy Rev. 2012;16(7):5131-45.
16.Atapour M, Kariminia HR, Moslehabadi PM. Optimization of biodiesel production by alkali-catalyzed transesterification of used frying oil. Process Saf Environ Prot. 2014;92(2):179-85.
17.Bashiri H, Pourbeiram N. Biodiesel production through transesterification of soybean oil: A kinetic Monte Carlo study. J Mol Liq. 2016;223:10-5.
18.Silitonga A, Masjuki H, Mahlia T, et al. Overview properties of biodiesel diesel blends from edible and non-edible feedstock. Renew Sustain Energy Rev. 2013;22:346-60.
19.Can Ö. Combustion characteristics, performance and exhaust emissions of a diesel engine fueled with a waste cooking oil biodiesel mixture. Energy Convers Manag. 2014;87:676-86.
20.Venkanna B, Venkataramana Reddy C. Direct injection diesel engine performance, emission, and combustion characteristics using diesel fuel, nonedible honne oil methyl ester, and blends with diesel fuel. Int J Energy Res. 2012;36(13):1247-61.
21.Moon G, Lee Y, Choi K, et al. Emission characteristics of diesel, gas to liquid, and biodiesel-blended fuels in a diesel engine for passenger cars. Fuel. 2010;89(12):3840-6.
22.Habibullah M, Masjuki H, Kalam M, et al. Biodiesel production and performance evaluation of coconut, palm and their combined blend with diesel in a single-cylinder diesel engine. Energy Convers Manag. 2014;87:250-7.
23.Sahoo P, Das L. Process optimization for biodiesel production from Jatropha, Karanja and Polanga oils. Fuel. 2009;88(9):1588-94.
24.Nabi MN, Rahman MM, Akhter MS. Biodiesel from cotton seed oil and its effect on engine performance and exhaust emissions. Appl Therm Eng. 2009;29(11):2265-70.
25.Ghanei R. Improving cold‐flow properties of biodiesel through blending with nonedible castor oil methyl ester. Environ Prog Sustain Energy. 2015;34(3):897-902.
26.Chavan SB, Yadav M, Singh R, et al. Production of biodiesel from three indigenous feedstock: Optimization of process parameters and assessment of various fuel properties. Environ Prog Sustain Energy. 2017;36(3):788-95.
27.Abedin M, Masjuki H, Kalam M, et al. Performance, emissions, and heat losses of palm and jatropha biodiesel blends in a diesel engine. Ind Crops Prod. 2014;59:96-104.
28.Capodaglio AG, Callegari A. Feedstock and process influence on biodiesel produced from waste sewage sludge. J Environ Manage. 2017;216:176-82.
29.Moecke EHS, Feller R, Dos Santos HA, et al. Biodiesel production from waste cooking oil for use as fuel in artisanal fishing boats: Integrating environmental, economic and social aspects. J Clean Prod. 2016;135:679-88.
30.De Pontes Souza D, Mendonça FM, Alves Nunes KR, et al. Environmental and socioeconomic analysis of producing biodiesel from used cooking oil in Rio de Janeiro. J Ind Ecol. 2012;16(4):655-64.
31.Passell H, Dhaliwal H, Reno M, et al. Algae biodiesel life cycle assessment using current commercial data. J Environ Manage. 2013;129: 103-11.
32.Taghizadeh-Alisaraei A, Hosseini SH, Ghobadian B, et al. Biofuel production from citrus wastes: A feasibility study in Iran. Renew Sustain Energy Rev. 2017;69:1100-12.
33.Hajjari M, Tabatabaei M, Aghbashlo M, et al. A review on the prospects of sustainable biodiesel production: A global scenario with an emphasis on waste-oil biodiesel utilization. Renew Sustain Energy Rev. 2017;72:445-64.
34.Zahed MA, Zakeralhosseini Z, Mohajeri L, et al. Multivariable analysis and optimization of biodiesel production from waste cooking oil. Environmental Processes. 2018;5(2):303-12.
35.Salehi A, Karbassi A, Ghobadian B, et al. Simulation process of biodiesel production plant. Environ Prog Sustain Energy. 2019;38(6): e13264.
36.Cao Y, Doustgani A, Salehi A, et al. The economic evaluation of establishing a plant for producing biodiesel from edible oil wastes in oil-rich countries: case study Iran. Energy. 2020;213:118760.
37.Feng L, Liu J, Lu H, et al. Techno-economic and profitability analysis of plant for producing biodiesel from fresh vegetable oil and waste frying oil on large-scale. Fuel. 2022;323:124304.
38.Ghobadian B. Liquid biofuels potential and outlook in Iran. Renew Sustain Energy Rev. 2012;16(7):4379-84.
39.Statista. Largest producers of CO2 emissions worldwide in 2016 based on their share of global CO2 emissions. Available from:https://www. statista.com/statistics/ 271748/ the-largest-emitters- of-co2-in-the-world. [Cited 10 September 2016]
40.Emissions GC. Available from:https://www. co2.earth/global-co2emissions. [Cited 20 November 2016]
41.Mathimani T, Kumar TS, Chandrasekar M, et al. Assessment of fuel properties, engine performance and emission characteristics of outdoor grown marine Chlorella vulgaris BDUG 91771 biodiesel. Renew Energy. 2017;105:637-46.
42.Karmakar A, Karmakar S, Mukherjee S. Properties of various plants and animals feedstocks for biodiesel production. Bioresour Technol. 2010;101(19):7201-10.
43.Singh A, He B, Thompson J, et al. Process optimization of biodiesel production using alkaline catalysts. Appl Eng Agric. 2006;22(4):597-600.
44.Al-Sakkari EG, Elozeiri AA, Abdeldayem OM, et al. Fish and animal waste as catalysts for biodiesel synthesis. Waste and Biodiesel. 2022:119-36.
45.Dharma S, Masjuki H, Ong HC, et al. Optimization of biodiesel production
process for mixed Jatropha curcas–Ceiba pentandra biodiesel using response surface methodology. Energy Convers Manag. 2016;115:178-90.
46.Moser BR, Vaughn SF. Biodiesel from corn distillers dried grains with solubles: preparation, evaluation, and properties. Bioenergy Res. 2012;5(2):439-49.
47.Hayyan A, Hashim MA, Hayyan M. Application of a novel catalyst in the esterification of mixed industrial palm oil for biodiesel production. Bioenergy Res. 2015;8(1):459-63.
48.Wakil M, Kalam M, Masjuki H, et al. Influence of biodiesel blending on physicochemical properties and importance of mathematical model for predicting the properties of biodiesel blend. Energy Convers Manag. 2015;94:51-67.
49.Chauhan BS, Singh RK, Cho H, et al. Practice of diesel fuel blends using alternative fuels: A review. Renew Sustain Energy Rev. 2016;59:1358-68.
50.Yilmaz N, Vigil FM, Benalil K, et al. Effect of biodiesel–butanol fuel blends on emissions and performance characteristics of a diesel engine. Fuel. 2014;135:46-50.
51.Al-Hamamre Z, Al-Salaymeh A. Physical properties of (jojoba oil+ biodiesel),(jojoba oil+ diesel) and (biodiesel+ diesel) blends. Fuel. 2014;123:175-88.
52.Phan AN, Phan TM. Biodiesel production from waste cooking oils. Fuel. 2008;87(17-18):3490-6.
53.Sadaf S, Iqbal J, Ullah I, et al. Biodiesel production from waste cooking oil: an efficient technique to convert waste into biodiesel. Sustain Cities Soc. 2018;41:220-6.
54.Saxena P, Jawale S, Joshipura MH. A review on prediction of properties of biodiesel and blends of biodiesel. Procedia Eng. 2013;51:395-402.
55.Ryan III T, Dodge L, Callahan T. The effects of vegetable oil properties on injection and combustion in two different diesel engines. J Am Oil Chem Soc. 1984;61(10):1610-9.
56.Hassan N, Rasul M, Harch CA. Modelling and experimental investigation of engine performance and emissions fuelled with biodiesel produced from australian beauty leaf tree. Fuel. 2015;150:625-35.
57.Atabani A, Silitonga A, Ong H, et al. Non-edible vegetable oils: a critical evaluation of oil extraction, fatty acid compositions, biodiesel production, characteristics, engine performance and emissions production. Renew Sustain Energy Rev. 2013;18:211-45.
58.Sbihi HM, Nehdi IA, Tan CP, et al. Production and characterization of biodiesel from Camelus dromedarius (Hachi) fat. Energy Convers Manag. 2014;78:50-7.
59.Azad A, Uddin SA, Alam M. Experimental study of DI diesel engine performance using biodiesel blends with kerosene. International Journal of Energy and Environment. 2013;4(2):265-78.
60.Moser BR. Biodiesel production, properties, and feedstocks. In Vitro Cell Dev Biol Plant. 2009;45(3):229-66.
61.Usta N. An experimental study on performance and exhaust emissions of a diesel engine fuelled with tobacco seed oil methyl ester. Energy Convers Manag. 2005;46(15):2373-86.
62.Bi C-h, Min M, Nie Y, et al. Process development for scum to biodiesel conversion. Bioresour Technol. 2015;185:185-93.
63.Azad A, Ameer Uddin S. Performance study of a diesel engine by first generation bio-fuel blends with fossil fuel: An experimental study. J Renew Sustain Energy. 2013;5(1):013118.
64.Acharya N, Nanda P, Panda S, et al. Analysis of properties and estimation of optimum blending ratio of blended mahua biodiesel. Engineering Science and Technology, an International Journal. 2017;20(2):511-7.
65.Hasan M, Rahman M. Performance and emission characteristics of biodiesel–diesel blend and environmental and economic impacts of biodiesel production: A review. Renew Sustain Energy Rev. 2017;74:938-48.
66.Atabani AE, Silitonga AS, Badruddin IA, et al. A comprehensive review on biodiesel as an alternative energy resource and its characteristics. Renew Sustain Energy Rev. 2012;16(4):2070-93.
67.Phan AN, Phan TM. Biodiesel production from waste cooking oils. Fuel. 2008;87(17):3490-6.
68.Ferris AM, Rothamer DA. Methodology for the experimental measurement of vapor–liquid equilibrium distillation curves using a modified ASTM D86 setup. Fuel. 2016;182:467-79.
69.Mohammadshirazi A, Akram A, Rafiee S, et al. Energy and cost analyses of biodiesel production from waste cooking oil. Renew Sustain Energy Rev. 2014;33:44-9